Solvent-Free Polyester-Type Polyurethane Systems
As environmental regulations tighten and the demand for sustainable manufacturing grows, industries worldwide are seeking to develop and adopt high-performance materials that are environmentally friendly and sustainable. Polyurethane, as a versatile high-performance polymer, plays a significant role across multiple industrial sectors. Its excellent mechanical strength, chemical resistance, and adhesion capabilities make it an ideal choice for coatings, sealants, and adhesives. Among its various types, polyester-type polyurethanes—known for their superior heat and hydrolysis resistance—are gaining popularity, especially in demanding environments requiring durability and longevity.
Despite these advantages, the ester bonds present within polyester structures are inherently vulnerable to hydrolysis, especially under conditions of high humidity and elevated temperatures. This susceptibility can impair the long-term stability of polyester polyurethanes, limiting their broader application in environments where water resistance and durability are critical. This inherent challenge has driven industry research and development efforts focused on enhancing the hydrolysis resistance of these materials, aiming to unlock their full potential for a wider range of demanding applications.
To address this issue, the industry has increasingly incorporated hydrolysis-resistant agents—particularly carbodiimide-based compounds. These agents stabilize the polymer chains by reacting with susceptible sites and forming protective barriers that prevent water ingress. This strategy has demonstrated remarkable success, leading to widespread adoption of carbodiimide-type hydrolysis-resistant agents in polyester polyurethane formulations, significantly improving water resistance, aging stability, and overall durability.
1. Features and Advantages of Polyester-Type Polyurethane
Polyester-type polyurethanes are synthesized by reacting polyester polyols with isocyanates, resulting in a polymer network characterized by ester linkages within the backbone structure. Compared to polyether-based polyurethanes, polyester variants are known for their exceptional mechanical strength, high thermal stability, and superior chemical resistance. These properties make them suitable for high-end coatings, adhesives, sealants, and elastomers used in environments subjected to mechanical stress and chemical exposure.
The ester bonds within these polymers confer a higher degree of rigidity and stability, especially at elevated temperatures. This robustness translates into excellent resistance to chemicals, oils, and solvents, making polyester polyurethanes ideal for demanding outdoor applications such as architectural coatings, marine sealants, and structural adhesives. Furthermore, their inherent durability ensures prolonged service life, reducing maintenance costs and providing peace of mind for end-users.
However, the ester linkage characteristic that confers these benefits also introduces a vulnerability: it is susceptible to hydrolysis when exposed to sustained moisture or humid environments. The ester bonds can break down over time upon water contact, releasing degradation products that weaken the material’s structural integrity. Therefore, improving the hydrolysis resistance of these materials is critical for expanding their applications and enhancing their market competitiveness.
2. Benefits and Challenges of Solvent-Free Polyurethane Systems
Traditional polyurethane formulations often rely on organic solvents to improve flowability and processability. While effective, these solvents are volatile organic compounds (VOCs) that pose significant environmental and health concerns, such as air pollution, toxicity, and smog formation. Increasingly strict environmental regulations and the push toward green manufacturing drive the industry to develop solvent-free or low-VOC polyurethane systems.
Solvent-free systems offer many advantages: they significantly reduce VOC emissions, meet environmental standards, lower manufacturing costs, and minimize waste and disposal issues. They also provide excellent weather resistance and mechanical strength, making them ideal for coatings, adhesives, and sealants.
Nevertheless, these systems pose technical challenges. Achieving proper flow and even dispersion, along with consistent curing, is more difficult without solvents, which often act as carriers. Controlling water content during processing and storage is critical because moisture can cause premature hydrolysis or hinder curing, negatively impacting bonding strength and long-term durability. In this context, incorporating hydrolysis-resistant agents becomes essential to ensure the stability and performance of polyester polyurethanes, especially under humid conditions.
3. Mechanisms of Hydrolysis-Resistant Agents
Hydrolysis-resistant compounds are crucial for improving moisture stability, particularly in solvent-free polyester systems. Among these, carbodiimide-based agents are renowned for their high chemical stability and reactivity.
Reaction Mechanism Between Carbodiimides & Polyester Polyols
Carbodiimides (CDIs) are highly reactive compounds used to enhance hydrolysis resistance in polyester-based polyurethanes. The primary reaction mechanism involves carbodiimides interacting with hydroxyl groups in polyester polyols. Specifically, the carbodiimide reacts with a hydroxyl group via nucleophilic attack, where the oxygen atom in the hydroxyl group attacks the electrophilic carbon atom within the carbodiimide’s isocyanate-like group. This nucleophilic addition results in the formation of a highly reactive intermediate—a urea linkage—through the creation of a carbamoyl-amidine structure.
In detail, the carbodiimide reacts with the hydroxyl groups to form an O-alkylated amidine intermediate. This intermediate can undergo further rearrangement or react to form more stable linkages. The carbodiimide effectively “reacts across” the ester bonds in the polyester backbone, replacing originally susceptible hydroxyl groups with more hydrolysis-resistant amidine structures. This chemical transformation results in the formation of urea and amidine linkages along the polymer chain, which significantly enhances the hydrolysis resistance of the material.
This reaction is facilitated by the electrophilic carbon within the carbodiimide, which readily reacts with nucleophiles such as hydroxyl groups under mild conditions. As a result, ester groups are stabilized, and crosslinking density within the polymer network increases. This enhanced network structure is more resistant to water attack, improving the material’s durability and hydrolysis resistance. Overall, the incorporation of carbodiimides into polyester polyurethanes creates more stable, water-resistant materials suitable for outdoor and humid environments.
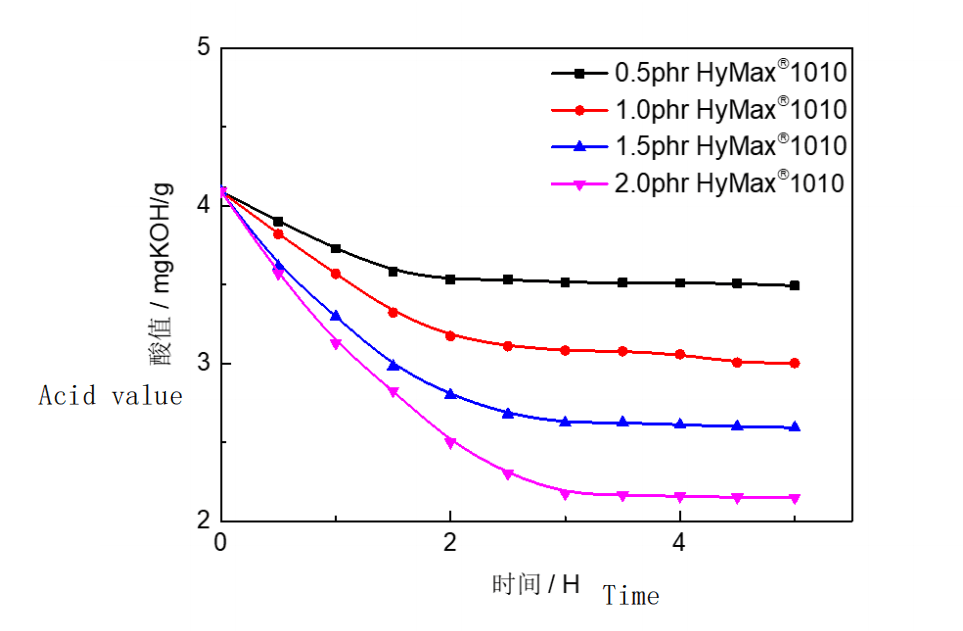
HyMax 1010 in polyester polyol
4. Practical Applications of Hydrolysis-Resistant Agents for Solvent-Free Polyurethanes
Research and industrial practice have demonstrated the effectiveness of hydrolysis-resistant agents in polyester systems that are solvent-free. For example, adding carbodiimide-based stabilizers to environmentally friendly adhesives can significantly enhance water resistance and adhesion reliability. This is particularly important in applications such as construction, transportation, and electronics, where long-term durability under humid conditions is critical.
These agents are also used in sealants and elastomers to prevent moisture ingress at interfaces. This improves weatherability and resistance to high temperatures, enabling products to withstand harsh outdoor environments and greatly extending their service life.
Moreover, hydrolysis-resistant agents can be incorporated into polyurethane films to improve their heat and water resistance. They also enhance interfacial adhesion, leading to increased durability. These optimized formulations produce high-quality protective coatings capable of performing reliably in extreme environmental conditions.
Overall, the strategic use of hydrolysis-resistant agents effectively broadens the application prospects of solvent-free polyurethanes. They provide environmentally friendly, durable, and high-performance solutions across multiple sectors, contributing to advances in sustainable materials.
5. Future Development Trends and Outlook
Looking ahead, future research will focus on increasing the efficiency of hydrolysis-resistant agents, developing greener synthesis methods, and creating multifunctional agents. Integrating nanotechnology—such as nanocapsules and nano-coatings—could enable controlled release of inhibitors, further enhancing barrier properties and durability.
Furthermore, there is a growing emphasis on developing environmentally benign, biodegradable, and low-toxicity hydrolysis-resistant agents that align with global sustainability goals. The application of advanced molecular design techniques will facilitate the synthesis of tailored molecules with superior water resistance, stability, and compatibility with various formulations.
As innovative technologies evolve, the scope of hydrolysis-resistant polyurethanes—especially in solvent-free polyester systems—will continue to expand, supporting high-end markets such as aerospace, automotive, and biomedical applications. These developments will help industry meet increasing demands for sustainable, high-performance, and durable materials that can withstand harsh environmental conditions while minimizing ecological impact.
In conclusion, the ongoing advancements in hydrolysis-resistant agents hold great promise for creating more durable, eco-friendly polyurethane systems, supporting the transition toward sustainable industry practices and high-performance materials capable of thriving in challenging environments.