With the increasing awareness of environmental protection, degradable mulch films have gained significant attention as an ideal substitute for traditional plastic films. These films are commonly made from polybutylene adipate terephthalate (PBAT), a biodegradable and processable material. However, PBAT mulch films exhibit poor hydrolysis stability in natural environments, making it difficult to precisely control their service life, which affects their actual performance. The introduction of carbodiimide hydrolysis resistance agents has provided an innovative solution to this issue.
Preparation Method of PBAT Degradable Mulch Film
Extrusion blow molding is the most commonly used method for preparing PBAT degradable mulch films. First, PBAT resin particles are mixed evenly with other additives (such as antioxidants, light stabilizers, hydrolysis stabilizers etc.) according to specific requirements. While PBAT resin has excellent film-forming properties, these additives are essential to optimize the film’s performance. Antioxidants prevent degradation during processing and use, while light stabilizers help reduce UV-induced damage.
The mixed material is then heated inside an extruder, where a rotating screw pushes it through a mold, followed by cooling and shaping. During extrusion, controlling process parameters such as pressure, temperature, and screw speed is crucial. The mold design determines the thickness and width of the mulch film.
- If the temperature is too high, PBAT may decompose, negatively impacting film performance.
- If the temperature is too low, plasticization will be incomplete, leading to poor film quality.
As the material exits the mold, an inflation device forms a film bubble. The blow-up ratio affects the microstructure and mechanical properties of the mulch film, and an optimal ratio is necessary to balance longitudinal and transverse properties. Once the film bubble cools and sets, it is stretched to the required size using a traction device and then wound into rolls, completing the production of PBAT degradable mulch film.
Reaction Principle of Carbodiimide Hydrolysis Resistance Agent in PBAT Mulch Film
The addition of carbodiimide hydrolysis resistance agents significantly extends the service life of PBAT degradable mulch films. However, the underlying reaction mechanism is complex.
PBAT contains ester bonds in its molecular structure. When exposed to water in humid environments, these ester bonds undergo hydrolysis, leading to molecular chain breakage and a decline in mulch film performance.
Carbodiimide hydrolysis resistance agents contain highly reactive carbon-nitrogen double bonds (-N=C=N-), which interact with water and carboxyl groups generated by PBAT hydrolysis. The mechanism works as follows:
- Water Reaction: Carbodiimide reacts with water, forming urea compounds, thereby reducing the presence of free water molecules in the system. This decreases water-induced damage to PBAT’s ester bonds.
- Carboxyl Reaction: Carbodiimide also binds to carboxyl groups produced during PBAT hydrolysis, forming stable amide bonds. This process prevents carboxyl groups from further catalyzing hydrolysis reactions, effectively repairing PBAT molecular chains and regulating its degradation process.
Application Effect of Carbodiimide Hydrolysis Resistance Agent
1. Extending Service Life for Agricultural Use
In agricultural applications, different crops have varying growth cycles, requiring mulch films with different service lives. For example:
- Corn Growth Cycle: Typically 90–120 days.
- PBAT Film Without Hydrolysis Resistance Agent: Can degrade within 60–80 days, failing to meet corn’s full growth needs.
- PBAT Film With Carbodiimide Hydrolysis Resistance Agent: Extends service life to 100–130 days, ensuring stable soil conditions, reducing water evaporation, inhibiting weeds, and maintaining soil temperature.
2. Improved Mechanical Properties
Field studies show that PBAT mulch films with carbodiimide hydrolysis resistance agents retain their mechanical strength far better than films without them.
- Comparison in tensile strength & elongation at break:
- Films without hydrolysis resistance: Faster mechanical degradation, becoming brittle and prone to tearing.
- Films with hydrolysis resistance: Retain higher tensile strength and flexibility, making them more resistant to external stress, tearing, and breakage.
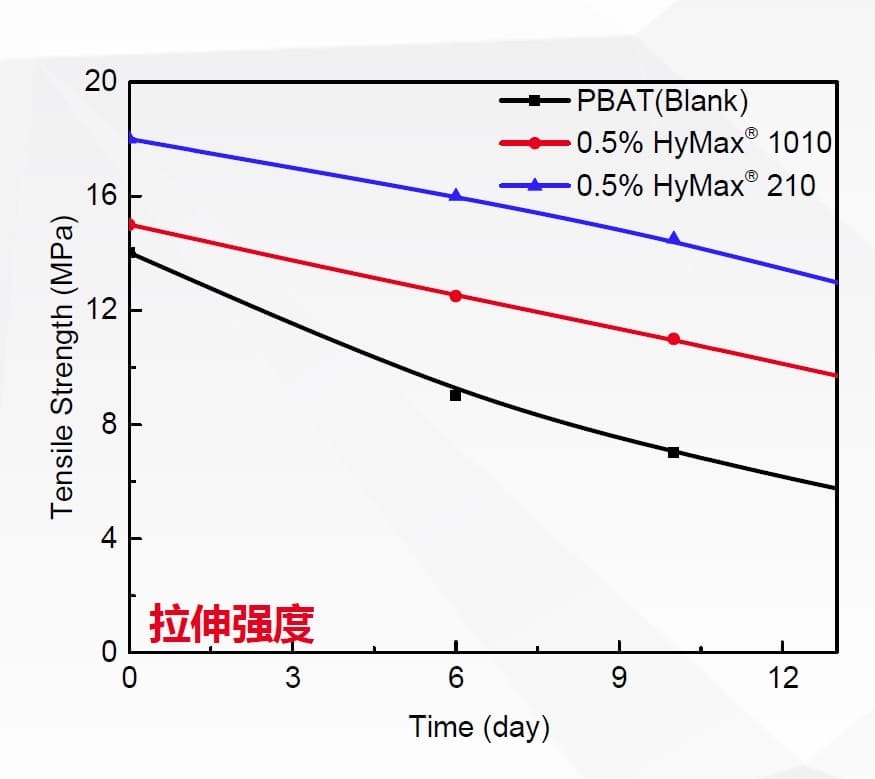
HyMax in PBAT
3. Maintaining Biodegradability
Importantly, adding a hydrolysis resistance agent does not interfere with PBAT’s biodegradability.
- Once the mulch film reaches its degradation phase, the hydrolysis resistance agent gradually loses effectiveness.
- Under microbial activity and environmental conditions, the film still degrades into harmless small molecules, returning to the natural ecosystem and meeting environmental protection standards.
Conclusion
Carbodiimide hydrolysis resistance agents offer a revolutionary way to regulate the service life of PBAT degradable mulch films. By:
- Improving hydrolysis resistance
- Enhancing mechanical durability
- Ensuring biodegradability
They enable PBAT mulch films to meet the diverse needs of agricultural applications, reduce plastic pollution, and promote sustainable farming practices.
As research and technology continue to advance, carbodiimide hydrolysis resistance agents are expected to be applied to a broader range of biodegradable mulch films, playing a crucial role in reducing plastic waste (“white pollution”) and advancing sustainable agriculture.