PU synthetic leather is widely used in car interior, sofas and other household applications because of its excellent wear resistance and comfortable feel, but the problem of hydrolysis has been troubling manufacturers, but also let the majority of users worry about the quality of the product. If these problems are not solved, it will largely limit the development of PU in the field of high-end household and automotive interiors.
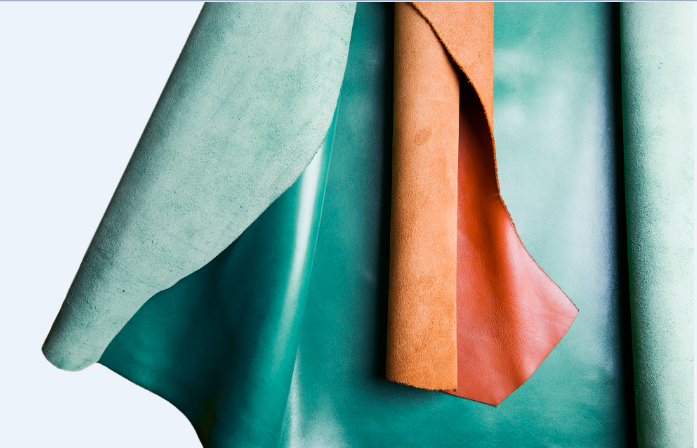
PU leather
The decomposition of polymers into small molecules in an environment of water and moisture is called hydrolysis.
PU synthetic leather is essentially a synthetic leather processed using polyurethane resin. The performance of the resin determines the final performance of the PU synthetic leather product. The hydrolysis resistance of the polyether type resin system is significantly better than that of the polyester type, the reason for this is that the linear polyester type polyurethane contains a large number of more polar ester groups and carbamate groups in the molecular chain segment which are prone to form hydrogen bonds, resulting in the product being more prone to absorb water vapour from the air compared to the product, the infiltration of a large number of water molecules into the polymer has an effect on the polymer in the following ways:
One type is reversible, i.e. the absorption of water and moisture by the polymer is reversible. When polyurethane absorbs water vapour from the air, the spacing between the macromolecular chain segments increases and the glass transition temperature of the material decreases, resulting in a plasticising effect, which softens, expands and then deforms the material.
The other category is irreversible, namely the hydrolysis of the polymer. The cracking of the macromolecules due to hydrolysis leads directly to a reduction in the tensile strength, modulus and hardness of the material and an increase in elongation at break, which in turn reduces the bond strength and leads to delamination and coating breakdown.
These two processes are carried out at the same time. In addition, the addition of acid, alkali or metal catalysts in the polymer synthesis process will lead to the intensification of hydrolysis, ester groups under the action of these catalysts and water reverse reaction, that is, hydrolysis reaction, polyester-type polyurethane hydrolysis after the production of carboxyl groups, the presence of carboxyl groups further as a catalyst for hydrolysis reaction, accelerate the hydrolysis reaction, resulting in further cleavage of the molecular chain.
Here, it is recommended that, in general, PU products must be dried after washing, and try to avoid using them in wet conditions. In addition, PU products should avoid washing with acidic or alkaline substances, such as soap and water used in life.
How do we solve these problems?
On the one hand, compared to traditional PU synthetic leather, CPU synthetic leather fundamentally changes the way the molecular chain segments are formed, from thermoplastic to thermosetting, i.e. from a linear molecular structure to a three-dimensional cross-linked structure, which prevents water molecules from intruding between the molecular chain segments and prevents water vapour from forming physical hydrogen bonds with the large polyurethane chain segments and then causing hydrolysis of the product. In addition, all CPU products are made from polyether resins, which further reduces the problem of hydrolysis in the resin system.
On the other hand, to further improve the hydrolysis resistance of the resin system, we can add a hydrolysis resistant additive such as carbodiimide to the resin system. The mechanism of action is that carbodiimide acts as an acid and water remover, effectively converting or neutralising the acid and water into a harmless urea-based structure, and can be embedded in the molecular chain segments to fill the cracking of the molecular chain caused by hydrolysis. This method is simple and easy to implement, the addition of carbodiimide does not require changes to existing equipment and production lines and has no impact on other properties of the material.
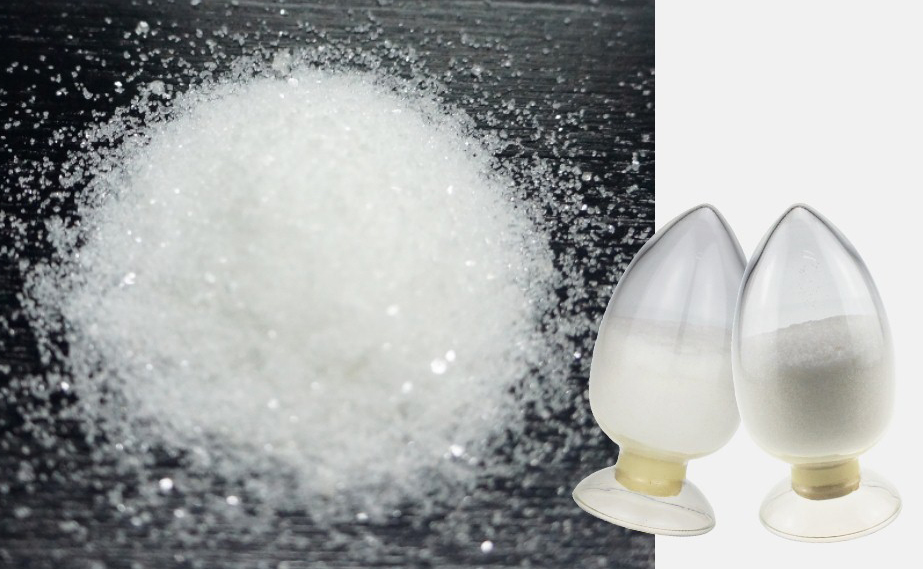
anti-hydrolysis agent
Langyi has accumulated many years of experience in the field of hydrolysis resistant addition to PU synthetic leather, and PU leathers with carbodiimide addition have improved their performance in terms of friction resistance, high temperature resistance and resistance to humid environment. We have also developed poly-carbodiimide crosslinkers suitable for the surface finishing of PU leather, which can be coated on the surface of PU leather to give it better resistance to wear, water, acid and alkali. If you need more information or free samples, please contact us.