The main purpose of adding additives to plastics is to improve processing performance, increase efficiency and reduce costs. Plastic additives occupies a small proportion in plastic materials, but they have a great impact on the quality of plastic products. Different types of plastics require different types and amounts of additives due to different molding processing methods and use conditions. The main used plastic additives are as follows:
1. Stabilizer
We all know that plastic products will fade, embrittle, and crack under the action of light, heat, oxygen and water during processing, storage and use. In order to delay and prevent the occurrence of aging, a plastic additive named as stabilizer must be added. The stabilizer mainly used to prevent heat aging is called heat stabilizer. The stabilizer mainly used to prevent oxidative aging is called antioxidant. The stabilizer mainly used to prevent light aging is called light stabilizer. The stabilizer mainly used to prevent hydrolytic aging is called hydrolysis stabilizer. They are collectively belong to stabilizers.
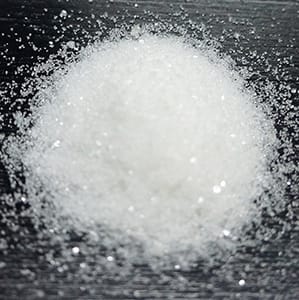
2. Plasticizer
Plasticizers can increase the flexibility, extensibility, and plasticity of plastics, reduce the flow temperature and hardness of plastics, and are beneficial to the molding of plastic products. The commonly used plasticizers are phthalic acid esters, sebacic acid esters, chlorinated paraffin and camphor.
3. Flame retardant
The additives that can improve the flame resistance of plastics are called flame retardants. Most plastics containing flame retardants have self-extinguishing properties, or slow down the burning rate. Commonly used flame retardants include antimony oxide, aluminum and boron compounds, halides and phosphate esters, tetrachlorophthalic anhydride, and tetraophthalic anhydride.
4. Antistatic agent
Antistatic agent plays a role in eliminating or reducing static electricity on the surface of plastic products. Most of the antistatic agents are electrolytes, and their compatibility with synthetic resins is limited, so that they can migrate to the plastic surface to absorb moisture and eliminate static electricity.
5. Foaming agent
Plastic blowing agent is a kind of low-molecular organic substance that can be vaporized at a certain temperature, such as dichlorodifluoromethane; or organic compound that decomposes into gas when heated. These gases remain in the plastic matrix to form a foamed plastic with many fine foam structures. Commonly used foaming agent are azo compounds, nitroso compounds and so on.
6. Coloring agent
Colorants are used to color plastics. It is mainly used for beautification and modification. About 80% of plastic products are colored into final products.
7. Lubricant
Lubricants are added to improve the release properties of plastics during thermoforming and improve the surface finish of products. Commonly used lubricants include: stearic acid and its salts, paraffin wax, synthetic wax, etc.
8. Reinforcing materials and fillers
In many plastics, reinforced materials and fillers occupy a considerable proportion, especially reinforced plastics and calcium plastic materials. The main purpose of this plastic additive is: in order to improve the strength and rigidity of plastic products, generally various fiber materials or inorganic substances are added. The most commonly used reinforcement materials are: glass fiber, asbestos, quartz, carbon black, silicate, calcium carbonate, metal oxides, etc.