3D printing is also known as additive manufacturing. Compared with the large-scale production of traditional manufacturing, 3D printing meets the needs of many customized products. Although the cost of the product is higher, the marginal benefit also increases. 3D printing materials are an important material foundation and key material for the development of 3D printing technology. With the development of the 3D printing market, the demand for 3D printing materials is also increasing.
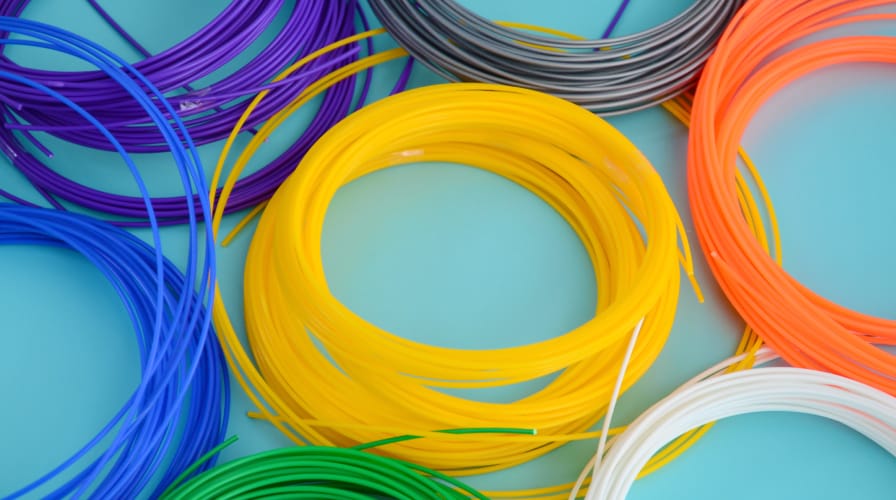
At this stage, with the advancement of technology and research and development, there are currently more than 300 materials available for 3D printing manufacturing. Thermoplastics such as ABS and PLA account for more than 50% of the consumables. At present, polymer material manufacturers mainly concentrated on ABS and PLA and nylon materials. According to statistics from Wohlers Prospective Industry Research Institute in 2016, 3D printing material PLA accounted for the largest proportion of 37.1%, followed by ABS, which accounted for 15.5%.
Polylactic acid (PLA) not only has good transparency, gloss, tensile strength and ductility, but also has unique biodegradability and biocompatibility, and its raw materials are mostly derived from plants (such as corn and potatoes). It is an ideal green and environmentally friendly 3D printing materials.
However, PLA as a 3D printing material still has some obvious performance defects. First, PLA materials are brittle and have poor impact resistance. Secondly, PLA materials have poor high temperature resistance, low heat distortion temperature, and poor dimensional stability of printed products in high temperature environments. Finally, PLA is easily hydrolyzed, and there is uncertainty in the degradation cycle.
For some products that require a long degradation cycle, the hydrolysis of PLA is an important issue. For example, bone scaffolds and industrial molds with a long service cycle require products to have a long degradation cycle. For this, by blending the anti-hydrolysis agent and PLA for modification, its anti-hydrolysis ability can be significantly improved, thereby prolonging the degradation cycle of the product.
For example, when PLA printing wire is boiled at 95℃ for about 8 hours, it will degrade. At this time, if 1.0% of the anti-hydrolysis agent HyMax®1010 is added to it, the failure time will be extended to 33 hours under the same boiled condition, which means the degradation cycle is extended by 4 times.
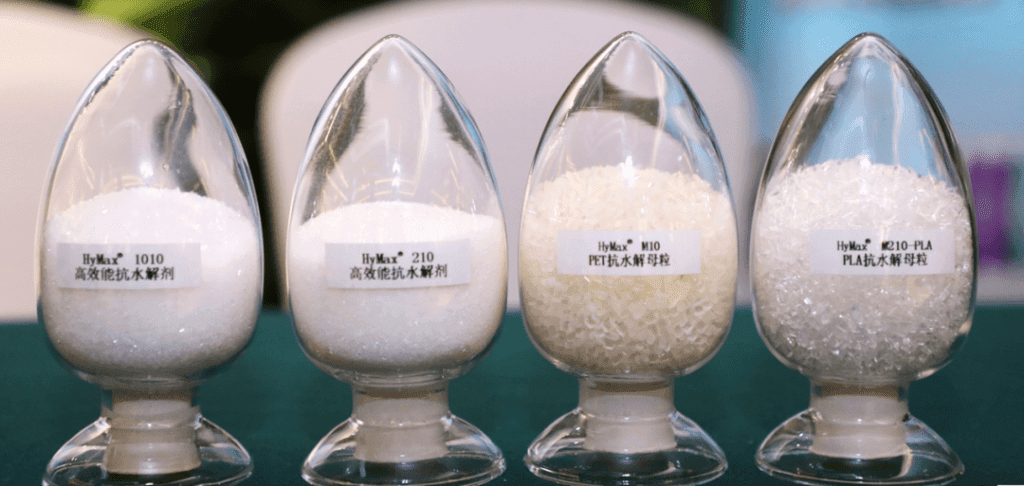
HyMax®1010 is a new, durable, and energy-efficient carbodiimide anti-hydrolysis agent. It can effectively capture the carboxyl groups of PLA molecules and react to produce urea-based compounds with no toxic side effects. In this way, it can effectively preventing PLA from rapid degradation which causes performance failure and lifespan decrease. In addition, by adjusting the amount of HyMax® added and the molecular weight, the mechanical properties and degradation rate of PLA can be adjusted.