With the maturity of new energy vehicles and autonomous driving technology, the market demand for automotive electronic materials is increasing. For example, the traditional automotive electronic materials basically have no flame retardant requirements, while the electronic materials used in new energy vehicles require flame retardant level. This presents a problem to vehicle manufacturers, automotive electronic component manufacturers and material suppliers.
In addition, new energy vehicles and driverless cars are using more electronic components than traditional cars. The heat dissipation is also greater. The continuous running time leads to the increasement of engine ambient peak temperature. So that the temperature resistance of the materials are held to higher requirements.
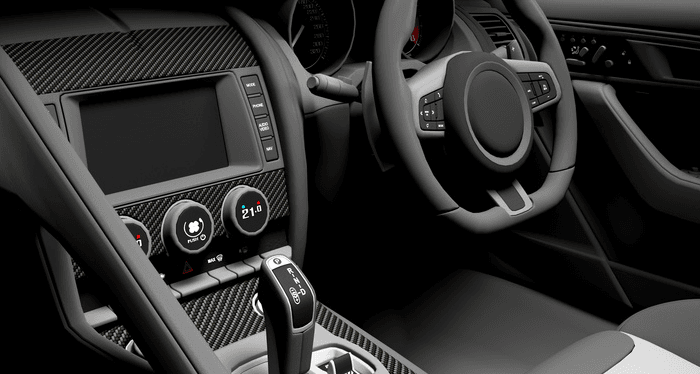
In the past, the automotive electronics industry usually use materials including nylon 6, nylon 66 and ordinary PBT materials, but these materials are no longer able to fit the automotive electronics industry today.
Although PBT has long been one of the common materials in the automotive electronics industry, its application scope is limited by its own water decomposition property. In addition, PBT injection molding processes require very stringent drying operations to ensure the quality and performance , which is also a challenge need to be addressed.
Factors affecting the heat and hydrolysis resistance of PBT
The factor that influences the heat and hydrolysis resistance of PBT is the concentration of terminal carboxyl groups. PBT contains ester bonds. The breakage of ester bonds occurs when PBT materials are in water at temperatures higher than its glass transition temperature. Then, the acidic environment formed by hydrolysis accelerates the reaction of hydrolysis, resulting in a dramatic decrease in performance of PBT.
Solutions for PBT heat resistance hydrolysis.
One is closing the end carboxyl group of PBT to reduce the concentration of end carboxyl group. For example, adding additives with epoxy functional group to seal the end by the reaction between the functional group GMA and the end carboxyl group of PBT.
Secondly, adding hydrolysis stabilizers, such as carbodiimide.
Hydrolysis stabilizers consume the carboxyl groups generated by hydrolysis, slowing down the acidic hydrolysis of PBT and improving the hydrolysis resistance of PBT resin.
Hydrolysis-resistant PBT products are superior to other PBTs in many aspects. The most significant advantage is the good retention of mechanical properties. Test result shows hydrolysis-resistant PBT products keep stable performance for up to 3,000 hours under USCAR Standard 3, 4, and 5 temperature/humidity environments and the 85°C and 85% relative humidity environments.
By adding anti-hydrolysis agent to make hydrolysis-resistant PBT is a good way to solve the PBT decomposition problem in water. Hydrolysis-resistant PBT can meet the requirements of temperature, humidity and flame retardant materials in the automotive electronics industry, and maintain good mechanical properties throughout the life cycle of electronic parts.